Photostory: Warren Wilson’s Blacksmithing
Quinn Bonney | November 10, 2021

Noah Lightsey, a junior, and a two and a half year blacksmithing crew member on ‘What is your favorite part of blacksmithing?’
“I’ve really enjoyed making some of the kitchen knives, mostly smaller cleavers. Partly because we use all recycled steel, usually off the suspension of cars and trucks. It’s nice to take a rusty piece of metal from the scrap yard and turn it into a set of nice, usable knives someone could use their whole life if they take care of them. It’s not a huge focus but blacksmithing the way we do it does intersect with the sustainability ethos of Warren Wilson College. Steel is the most recyclable material around; it’s nice to take it off abandoned car chassis and turn it into something cool or functional tools that we then use to make more tools.”
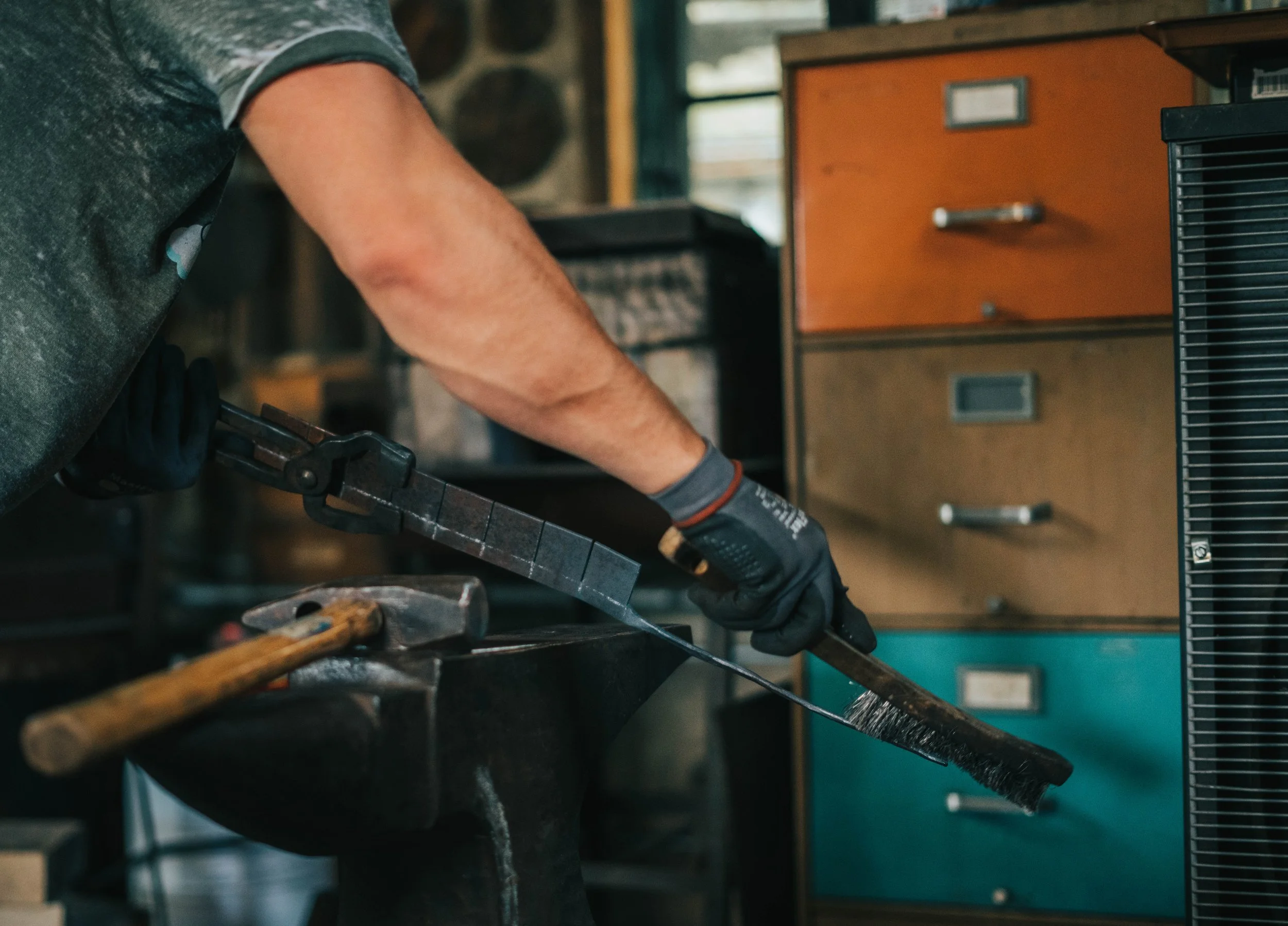
Tim Kinsey using a standard wire brush to knock off any loose steal. He is working on the stem on a soon-to-be rose.

Kinsey using a propane-run forge, which is the most popularly used forge in common blacksmithing. It’s great for large projects that need completely even heat.

Kinsey working on straightening out the stem of a soon-to-be rose.

Lightsey using a coal forge, a basic construction with a cast-iron pit with a hole in the bottom. The hole provides an upward blast of air for the coal. The coal basin has fabricated pans around to hold more fuel and tools. For ventilation, the coal forge has a fabricated sheet metal chimney.

Hammering out the boss of the hook, which is the flat spot where you’d drill two holes to mount it.

Lightsey using wood rasps to get the handle to fit the eye of the hammer.
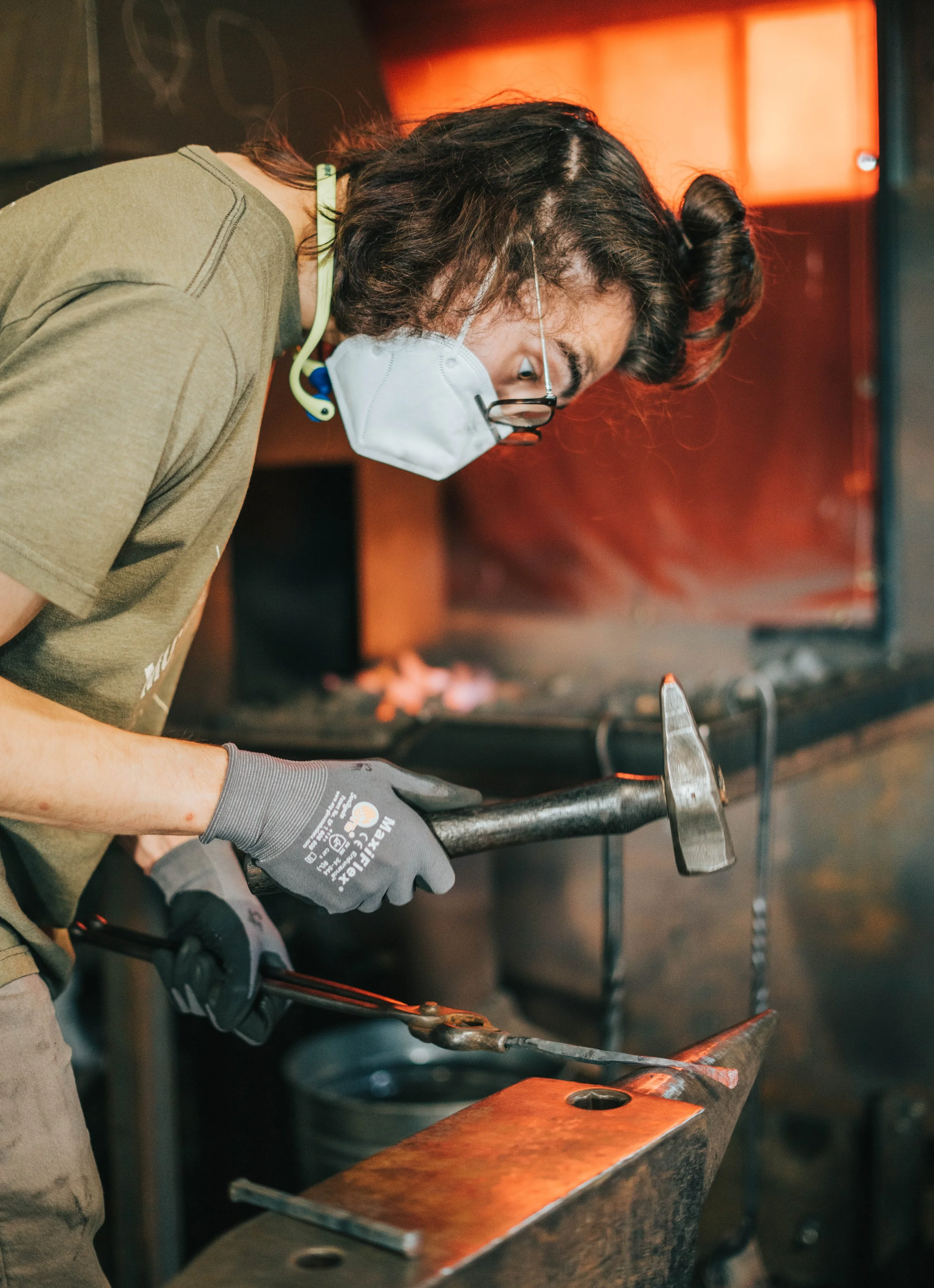
Sam Elston drawing out the material over the horn of the anvil, compressing it on multiple sides to force some more length into it.

What blacksmithing does has changed over the last few years. It’s always been involved in small repairs like straightening out lawn mower blades or repairing plows. Recently, however, the crew has been taking on larger fabrication projects for the farm.
“We made a big plate steel grain hopper for chicken feed that's now out in the pasture by the white barn,” said Lightsey.
The crew is also planning on making a hay baler by the end of this school year.

Lightsey when asked ‘What do you wish the student body knew about blacksmithing?’
“We are sequestered in our own little world down there, but the shop is almost open to anyone if someone wants to come down and check out the space. We are always happy to schedule people to come in and make things; it's open to everybody. We just don’t do a great job of getting the word out about that. We host open forges and events, which we haven’t had many of since the pandemic hit but are getting back into it again. We try to provide a comfortable and enjoyable space for anyone interested in craft on campus.”

Lightsey squaring up the block of steel with the power hammer.
“It’s a Fairbanks Company power hammer manufactured in 1916, it’s almost all original except that it was originally supposed to run the treadle mechanism (a lever worked by the foot to impart motion to the machine) off a steam driven shaft. Since we don’t have a steam engine we fitted a little motor to the back,” said Lightsey.

Lightsey using a block wire brush to scrape some of the scale off of the outside of the piece. Scale is little layers of oxide that forms in the fire and brushing keeps the surface clean and keeps the scale from eating away and making pits on the piece.
“It’s almost like a rust that is happening really quickly because of the amount of oxygen hitting the metal in its molten, excited state.”

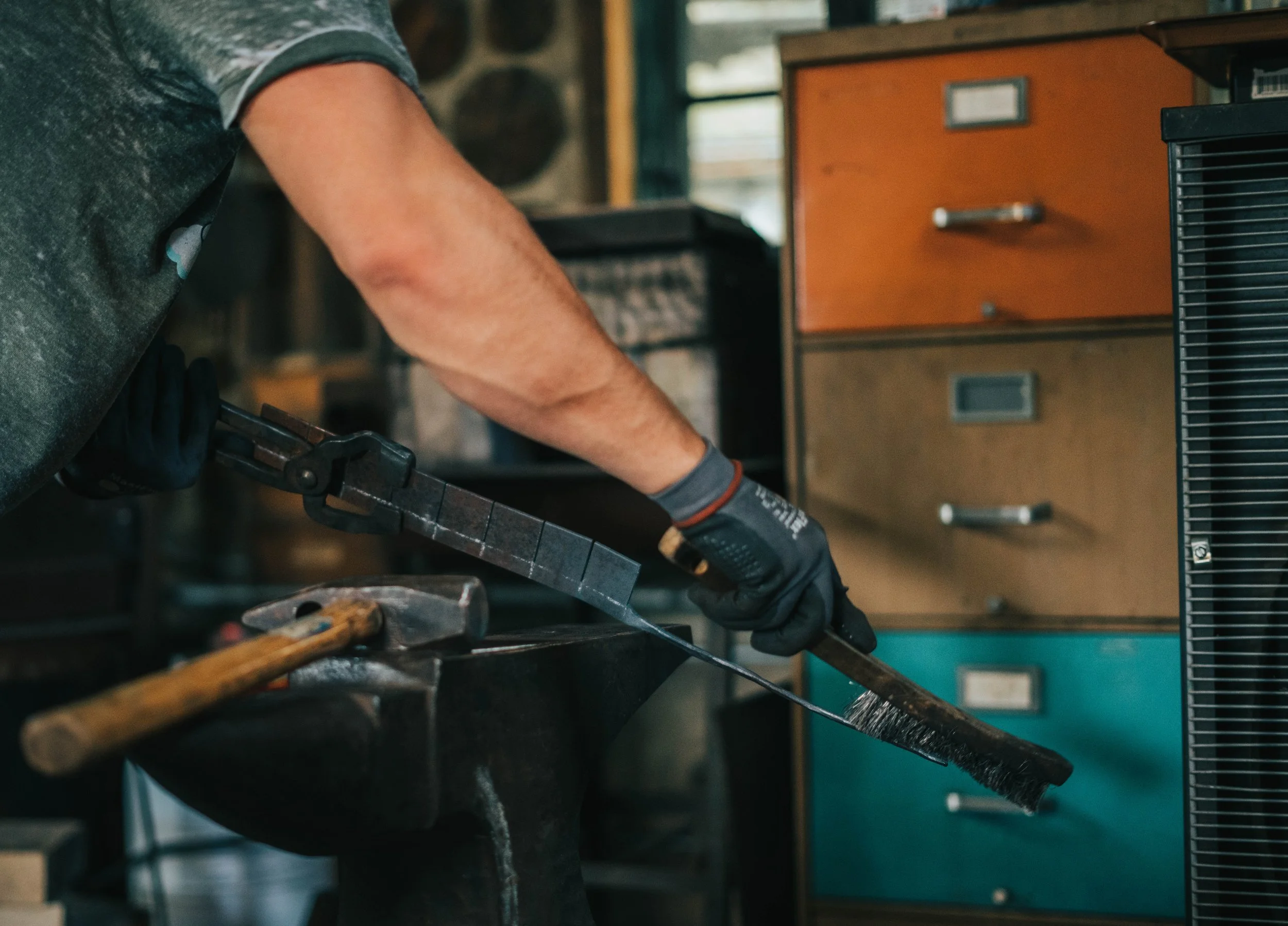





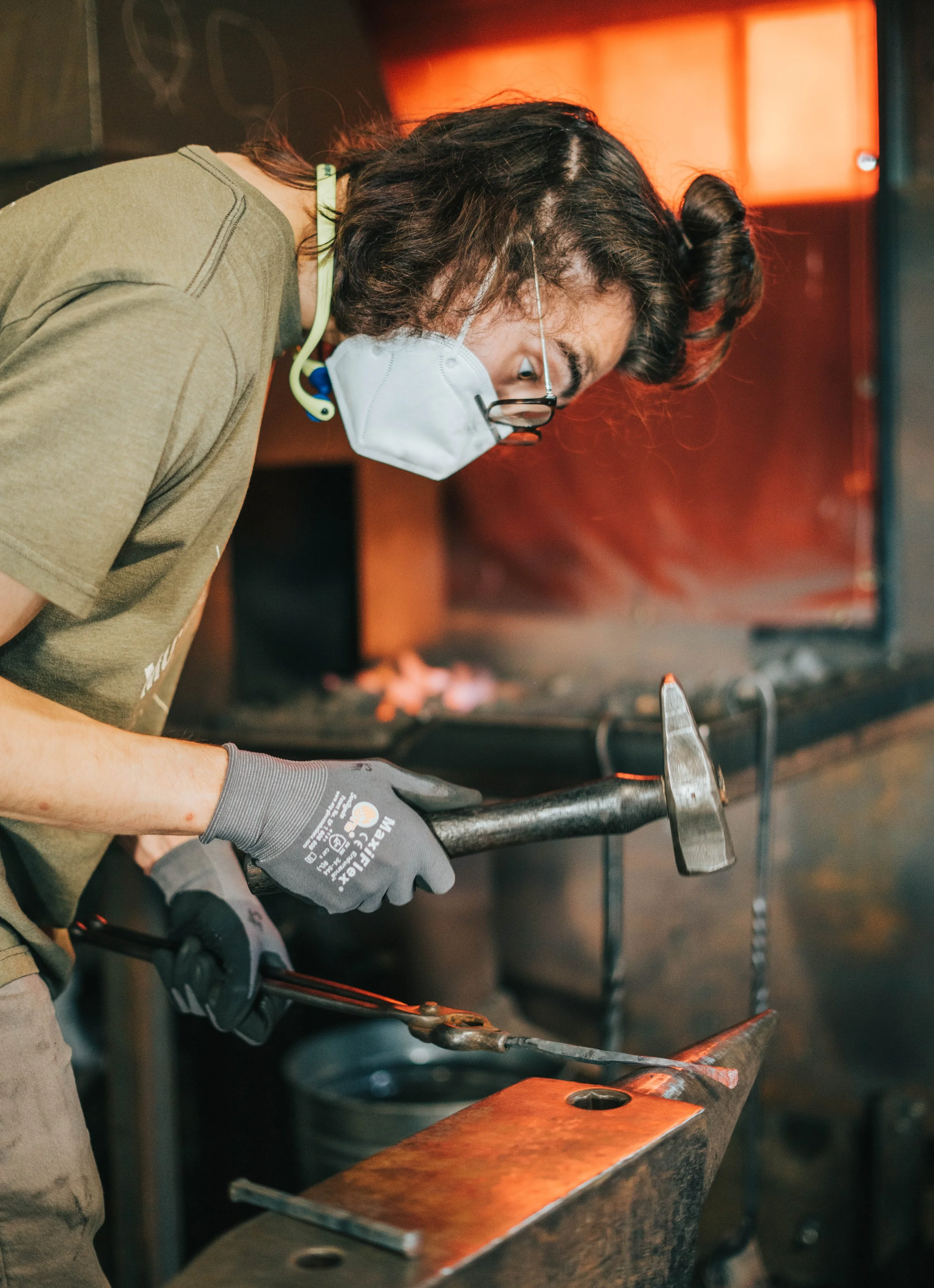



